Digital Transformation is a common buzzword reverberating across the innovation centers of global corporations that seek to radically transform and reinvent their Operations, products & services in a manner that generates an unparalleled level of customer satisfaction. Digitizing the areas of the enterprise, those which will maximize the business impact has become paramount due to increase in global competition, increasing sophistication in customer preferences and not to mention exponential evolution of technologies like Big Data, Artificial Intelligence, Cloud Computing, Internet of Things (IoT). In the Year 2019 alone the Global spend on Digital transformation amounted to approximately $1.3 trillion.
Now arriving at the key agenda of this write up, that is to explore specifically the state of Digitization of India’s manufacturing sector, what is done, what can be done and what must be done. The growth of this sector is critical for the resurgence of growth in the Indian Economy as its current Gross Value Added (GVA) is estimated at $397.14 Billion as of FY20. For this value grow at an unprecedented rate further, adoption of Advanced Digital Production Technologies (ADP) is inexorable.
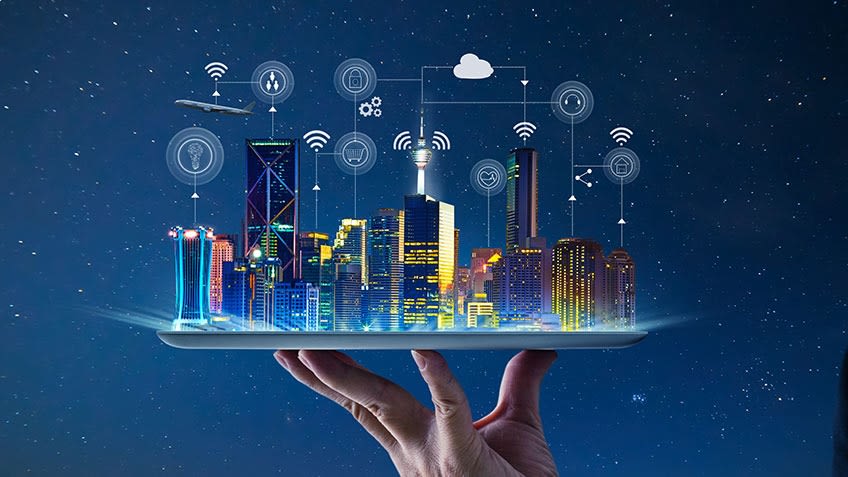
The United Nation’s Industrial Development Organization (UNIDO) released its Industrial development report on “Industrializing in the Digital Age” which assesses the development and application of ADP technologies, here the assessment found only 10 global frontrunners including Germany, Japan, Republic of Korea, UK and USA, India made it into the list in the second group of leading economies along with countries like Australia, Canada, Singapore, and Spain. It’s in the view of the fact that there has been an increase in the number of patents on ADP technologies filed by Indian Research Centers while even embedding them in the Shop floor Operations. Before we go further it’s necessary that we understand digitally transforming the operations needn’t always translate digitizing each every aspect, but only those areas which maximize business impact.
What is done so far in Digital Transformation of Indian Manufacturing?
Many Multinational Corporations who have their factories in India and some Indian companies from the have recognized the potential of Technologies like Industrial IoT, Robotics, Manufacturing Execution systems, Augmented Reality (AR) in conjunction with Superior Data storage facilities and Analytics platforms to derive value out of the data.
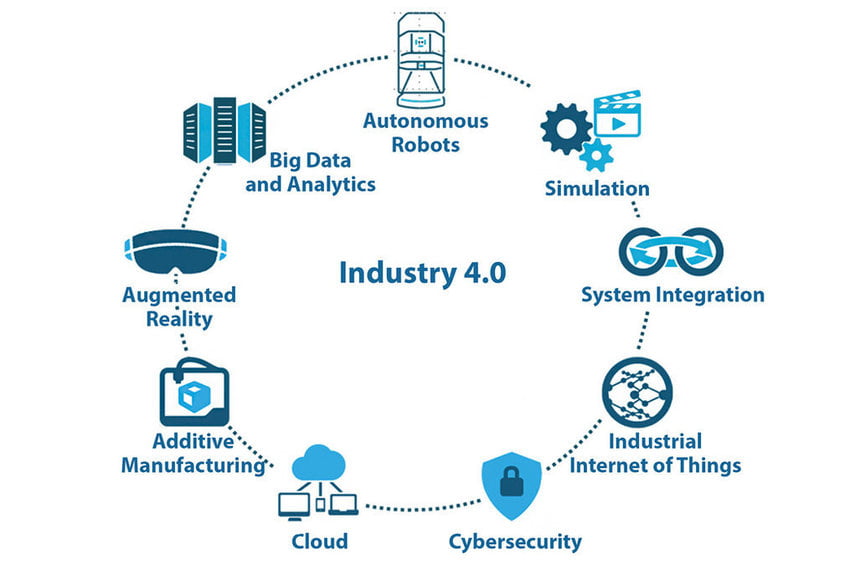
The present technological aspects which manufacturers assess pertain to data sourcing, reliability of the data, maintaining a seamless flow of crucial Data across the whole value chain in a tenacity that streamlines & bolsters the production systems efficiency and effectiveness, basically evaluating the whole structure of Information Systems. More so now than in the past three decades have the Operations challenges have spurred to be more vexing and convoluted in the backdrop of rise in consumer demand, global competition, increasing product lines and global Supply Chain Management.
Material Handling is a hazard prone task, so to ensure safety material flow is automated through Automatic Guided Vehicles (AGVs), which turned out also reduced waiting time while slashing losses which were earlier incurred due to the waiting time. Now Material movement is scheduled and optimized through the use of Manufacturing Execution Systems (MES) and Industrial IoT, the Data entries at the backend of manufacturing Processes is automated through Robotic Process Automation (RPA) Softwares.
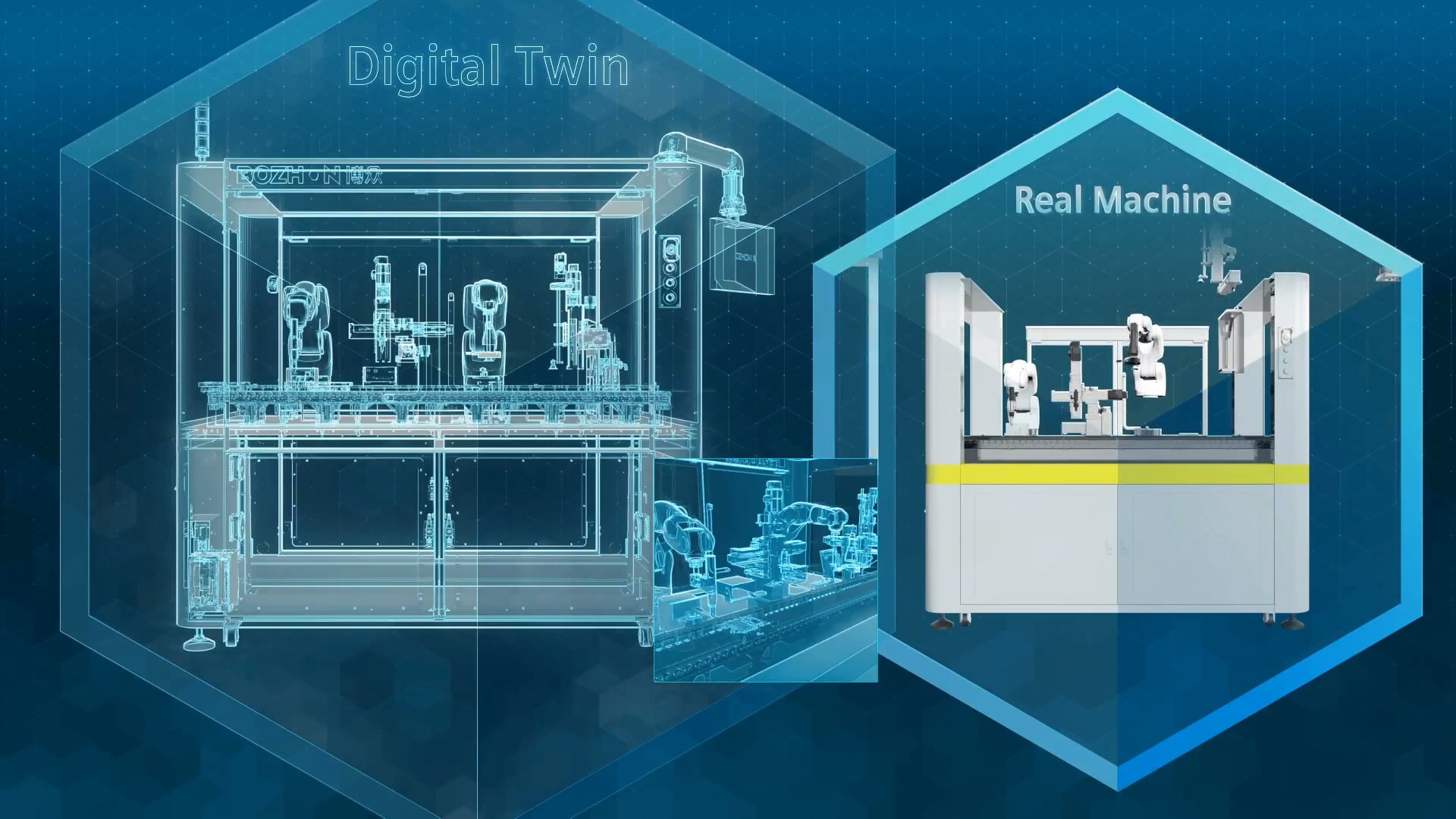
Organizations which undertake the manufacturing of Large equipment’s like Industrial Air conditioners and wind turbines guide their design process through Augmented Reality (AR) and Digital twins so as to graphically simulate the whole equipment to reconfigure certain sub components ,in this manner they can drastically slash costs which otherwise would have been incurred for reworking on the design.
Namely companies like Godrej, Mahindra & Mahindra, Indian Oil Corporation, Parle, Mother Dairy and some other large scale manufacturers have embraced this transition ordained by Industry 4.0 through fervently incorporating all the critical automation systems, Data analytics capabilities driven by AI/ML algorithms , decision optimization solutions and logistics intelligence in their fabric of operations. However we must be observant of the fact that these companies are far outnumbered compared to those manufacturing enterprises who still rely on outdated machinery and information systems or rather we can say paper based means of operating.
This Notion can be intuitively likened to the idea of an automation island where handful of companies have transformed their operations while a large swath of others still predicate their processes on traditional methods.
What can be done for a complete embrace of Digital?
It is apparent that there is a broad gap between the global Manufacturers adoption of Advanced Digital Production (ADP) technologies and Indian manufacturer’s adoption of the same, nevertheless India now ranks 44th in the Digital Competitiveness rankings as of 2019 which points at a great potential to vociferously internalize ADP technologies as a cornerstone of all Shop floor Operations.
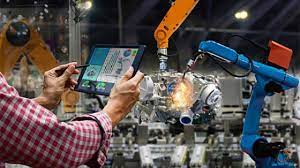
There is a conventional conditioning pervading the strategic decision processes of these medium and small scale manufacturers that regardless of expansion capabilities, short term profits must be maximized at any cost thus deterring away from any long term possibility of investing in technologies for long term growth prospects. Reconfiguration of such a narrow narrative is important. Producer’s investment in ADP technologies is rooted in the dichotomy between exploiting on the core and exploring new change opportunities. Every successful digital transformation is 1000 times more demanding in entirely rethinking the existing shop floor operations which we can understand to be Data driven, Automated at every critical workstation such that the cycle time is reduced, purely process oriented as opposed to outcome oriented for great quality. The process design and product design are highly consequential aspects of how the product is perceived by the user. Here Data Analytics is key so the metrics should be defined for the success of every step of the process and configured in the analytics platform while collecting the equipment and workstation data through IoT sensors. The most important use cases of this system are predictive maintenance, predictive capacity expansion, Quality information system (QIS) and customer data analysis.
However it must be ensured that the right data infrastructure is in place, that which can collect, organize, integrate data in an efficient manner. Furthermore creation of data silos must be avoided while data interoperability must be endorsed across the organization because a common repository for collecting data for different functional uses saves cost, creates data provenance and most importantly saves time.
Customer survey data highlights what customer believes are Critical to Quality (CTQs) of the product then this data must be transmitted to the production and purchase department so as to measure the existing practices and establish the standards to achieve the CTQs, this exemplifies the merits of data interoperability. These tasks now can be streamlined through Manufacturing Execution Systems (MES) which use machine learning by analyzing all the parameters and optimizing the existing processes to maximize the customer satisfaction thus bringing more Revenue and saving costs on labor overtime, reworking, warranty and defect reduction.
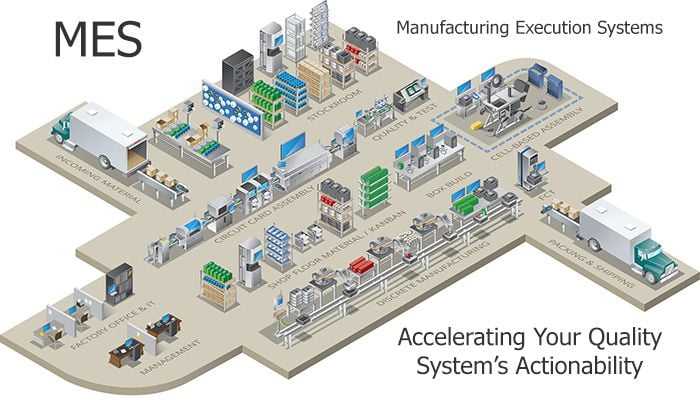
MES is a computerized system which connects to multiple machines, controllers, sites, and vendors to transmit real time production information and integrate easily with enterprise applications, thus enables complete visibility, control of production processes across the enterprise.
Having worked as an intern for an Industrial automation company which develops solutions on wearable technology for remote work operations like training, maintenance and machine installation it became clearer that Automation is the key for manufacturing growth post Covid-19 pandemic.
These propositions derive support from the fact that India’s Industrial Automation Sector is poised to grow at Compounded Annual Growth Rate (CAGR) of 11.6% till the year 2023 and India’s Manufacturing Sector is expected to account for 25-30% of GDP by FY2030.
Now it is arguable that all manufacturing enterprises might not possess the financial resources to expedite such a large undertaking so here it becomes more instrumental to have a strong grasp of what the enterprise believes are its core competencies.
What must be done?
Reflecting on the core competency statement it is a call for action through enterprise introspection so as to ascertain what are the most economical ways can a small enterprise go digital by leveraging on what it recognizes as its core competency. This challenge is mostly pertaining to the Indian context because of risk appetite of Indian financial institutions to give loans to small enterprises to finance this transformation.
However ‘Make in India’ initiative can really turn things around as it gives rise to startups that provide B2B platforms for manufacturers at an affordable cost. This might indirectly save the manufacturer the cost of reaching out to customers and will also connect to a large network of suppliers. So the producer must use these ecommerce platforms as a path for digitizing its customer reach tasks, as they now can now get customers which are scattered across vast geographies while logistics platforms facilitate the trade through warehousing, distribution, packing and other auxiliary services.
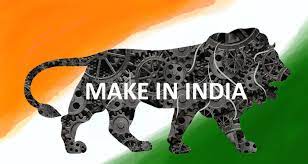
Having skillful people is central for effectuation of these capabilities which in India becomes a challenge since very small fraction of educated population can work on such programs, here the enterprises can establish a strong relationship with skill development institutes which teach programming languages, analytics, using enterprise software and agile management.
Every Manufacturing enterprise regardless of its size must ask itself reflective questions which have far-reaching business impact
1. What are our core competencies that can guide our path towards incorporating digital technologies to scale our business and expand our reach?
2. Are we allocating our financial resources enough towards all those technologies which will develop our value chain
3. What efforts are we taking towards Digitally reconfiguring our process to offer our customers great quality products?
4. Which processes must be automated and what must not be? Which processes can we do away with?
5. Will our business be relevant if follow our conventional wisdom in this digital age? If not then how and who might disrupt us?
6. What are the environmental factors that are or might hinder our growth?
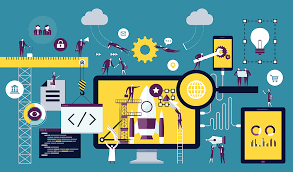
These consequential questions may offer Indian Manufacturers a Clear roadmap for their Digital transformation Journey. So we can infer that Digital Transformation is not just about adopting technologies but rather about assessing the existing business capability and discerning what combination of these technologies might expand and optimize the current production capacity while Generating Unparalleled levels of customer satisfaction by delivering innovative products.
Conclusion
This article is an attempt to expand my existing understanding of Digital Transformation in the Indian Manufacturing context. I have not gone deep in the technology aspect as we first have to assess our business practices and reconfigure our current business objectives to be more global. While it may not cover the entire picture and possibly could even be wrong in certain aspects but it still offers a moment to think critically on what is and what could be? Being an Operations Management Student I strongly feel that all the traditional manufacturing practices must be entirely disrupted by an open embrace of Emerging technologies to achieve excellent levels of operational performance which translates into customer satisfaction and increased returns to the bottom line.